Un flux tiré est une organisation dans laquelle c'est la demande du client qui déclenche la mise en fabrication d'un produit ou le démarrage d'une prestation de service. Ce concept est évoqué en Lean Management et en Lean Manufacturing et constitue une étape importante dans l'amélioration des processus d'une entreprise.
Dans certains contextes industriels, cela nécessite de mettre en oeuvre des changements radicaux et de faire preuve d'innovation.
Dans cet article, je vous propose une première approche de ce concept. Nous allons voir en quoi il consiste et quels sont ses principes, nous allons identifier ses principaux challenges de mise en oeuvre, puis nous allons voir comment le mettre en place en 8 étapes.
Définition du flux tiré
Dans le contexte de l'entreprise, la définition du flux qui nous intéresse est la suivante : il s'agit d'éléments circulant dans l'entreprise et destinés à être utilisés et transformés au cours du cycle d'exploitation.
Ce flux influence directement la manière dont la planification et l'ordonnancement sont effectués, pour répondre efficacement à la demande réelle du marché.
Trois sortes de flux circulent dans l'entreprise :
- Les flux physiques
- Les flux d'information
- Et les flux monétaires
Dans cet article, nous nous intéresserons principalement aux flux physiques : par exemple, des lignes de fabrication de machines à laver.
Mais les thèmes abordés sont applicables également à des flux d'information : par exemple, la communication de la liste des trains disponibles pour effectuer un trajet que vous voulez réserver.
La cartographie VSM (Value Stream Mapping) que nous avions vue dans un article précédent permet d'analyser un flux en représentant à la fois sa version actuelle et la cible visée.
Quelle différence entre flux poussé, flux tiré et flux tendu
Définissons ici ces trois notions distinctes :
1) Flux poussé
Dans un flux poussé, les éléments circulent au rythme imposé par un moyen de production situé en amont ou par les livraisons d'un fournisseur.
Par exemple, la production de conserves de haricots va suivre le rythme de la cueillette de ces légumes arrivés à maturité.
Un flux tiré est une organisation dans laquelle, c'est la demande du client qui déclenche la mise en fabrication d'un produit ou le démarrage d'une prestation de service.
2) Flux tiré
Dans un flux tiré, les éléments circulent au rythme de la demande des clients ou d'un poste de travail situé en aval.
Par exemple, dans une pâtisserie, la préparation du gâteau marqué "Bon anniversaire Florian" sera déclenchée par la commande du client et en fonction de la date à laquelle le client a prévu de venir chercher son gâteau.
3) Flux tendu
Un flux tendu "au sens strict" est un flux dans lequel il n'y a aucun stock intermédiaire entre les différents postes de travail impliqués dans le traitement des éléments circulants.
Un poste de travail situé en amont ne réalise son opération que lorsque le poste de travail situé immédiatement en aval est prêt à recevoir l'élément pour le traiter à son tour.
Le flux tendu est un cas particulier du flux tiré, puisque pour ne pas avoir de stock, il est nécessaire d'avoir reçu au départ une demande provenant du client ou de l'aval. Par contre, le flux tiré n'est pas nécessairement un flux tendu car il est accepté dans ce cas d'avoir certains stocks intermédiaires limités, contrôlés et managés.
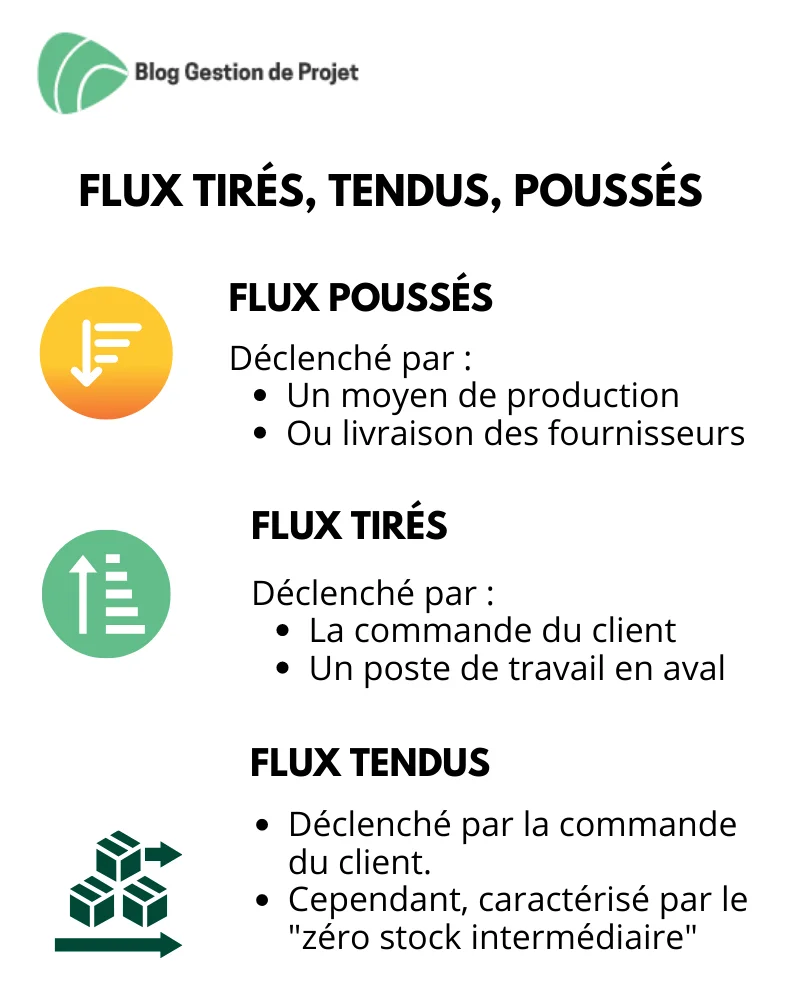
Caractéristiques d'un flux tiré
Comme nous l'avons vu en introduction, il s'agit d'une organisation dans laquelle, c'est la demande du client qui déclenche la mise en fabrication d'un produit ou le démarrage d'une prestation de service.
1) Initié par la demande du client
Cela signifie donc qu'un intervenant ne commence à réaliser ses opérations que lorsque le client a transmis sa commande.
2) Déclenché via un système visuel
Cela implique également la mise en place d'un système visuel permettant à un poste de travail "aval" de faire déclencher les opérations du poste de travail "amont" en fonction des besoins et dans l'ordre des besoins.
C'est ce que l'on appelle un système Kanban.
3) Sait "s'arrêter" sans mauvais impact
Cela signifie qu'il doit "savoir s'arrêter" lorsque la demande s'arrête. C'est-à-dire qu'il existe une flexibilité permettant de stopper à tout moment un poste de travail sans conséquence négative pour l'entreprise ou pour les intervenants.
Pourquoi mettre en place le flux tiré ?
Nous l'avions vu : le Lean est une démarche orientée Client dont l'un des principes fondamentaux consiste à se focaliser sur ce pour quoi le Client est prêt à payer.
Piloter les flux en fonction de la demande du client va ainsi contribuer à ancrer dans l'entreprise le fait de mettre le Client au centre de l'organisation.
Le fait d'être piloté par la demande des clients va permettre de diminuer et de stabiliser le "temps d'écoulement", c'est-à-dire le temps qui s'écoule entre le moment où le client passe sa commande et celui où il reçoit ce qu'il a demandé.
C'est un des critères différenciants qui améliorera la satisfaction client et qui peut donner un avantage concurrentiel.
Comme tout ce qui est produit correspond à une demande immédiate de l'aval, les stocks intermédiaires vont diminuer, ce qui génère un gain financier pour l'entreprise : moins d'espace de stockage à utiliser, moins de manipulations logistiques, moins d'immobilisation d'actifs.
L'avancement du flux et le suivi des commandes sera plus facile à maîtriser.
Enfin, la détection des défauts sera facilitée et plus réactive du fait que les éléments passent plus rapidement d'un poste de travail au suivant.
Un défaut identifié ne nécessitera de rebuter ou de retravailler qu'un nombre limité d'éléments, contrairement aux flux constitués de stocks importants au sein desquels la recherche d'éléments défectueux peut être longue, fastidieuse et très aléatoire.
Ainsi, le flux tiré permet d'optimiser les stocks et de réduire les coûts, et d'optimiser la qualité et les délais.
Cette triple contrainte est celle qu'on retrouve dans le concept de la maison Lean illustrée ci-après :
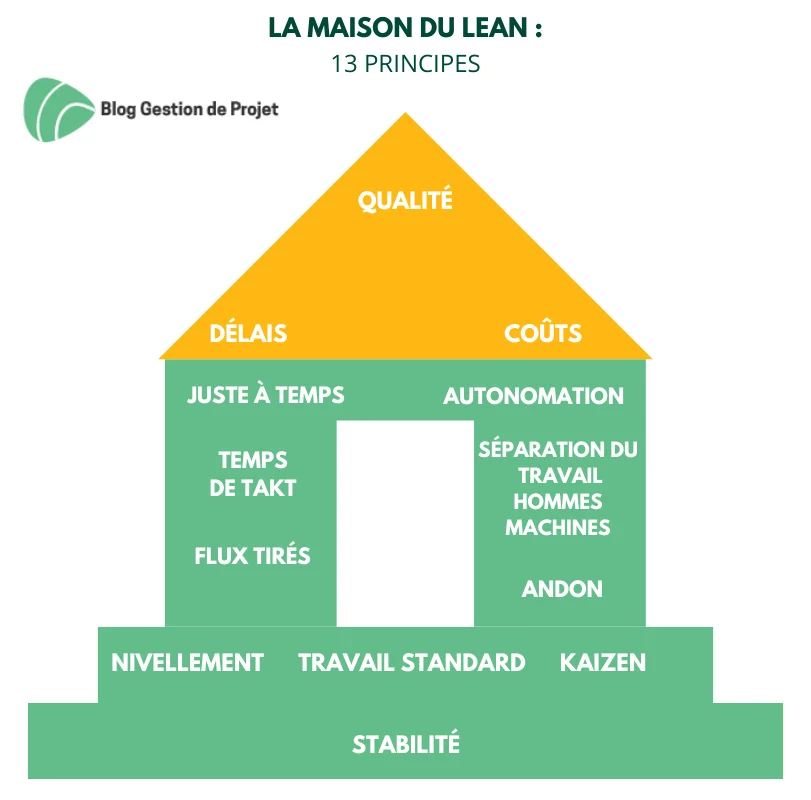
Challenges liés au flux tiré
La mise en place du flux tiré vient avec un certain nombre de défis qu'il essentiel de considérer :
1) Les problèmes sont visibles plus rapidement
Comme les stocks intermédiaires sont très réduits voire inexistants, un incident sur une étape du flux, par exemple une panne de machine, va impacter beaucoup plus rapidement l'ensemble de la production.
Le flux tiré rend ainsi visibles et insupportables des problèmes qui existaient déjà précédemment et qu'il va falloir à présent résoudre.
C'est donc à la fois un challenge, mais aussi un aspect vertueux dans le cadre d'une démarche Lean d'Amélioration Continue.
2) L'impact du temps de changement de série est plus important
Le fait de s'adapter quasiment en temps réel à la demande des clients va nécessiter de faire des "changements de série" beaucoup plus fréquemment.
Par exemple un fabricant de tubes en acier, au lieu de fabriquer dans la journée 1000 tubes de diamètre 450 mm et d'épaisseur 15 mm, va fabriquer 200 tubes de diamètre 450 épaisseur 15, + 200 tubes de diamètre 450 épaisseur 12, + 200 tubes de diamètre 380 épaisseur 10, etc...
Ces opérations de changement peuvent nécessiter du temps et de la main d'œuvre.
En accompagnement d'un passage en flux tiré, il est donc utile de mener une démarche dite "SMED" qui consiste à diminuer les temps de changement de série et à simplifier ces opérations.
3) Une formation et un accompagnement sont incontournables
La mise en place de ce type de flux engendre la plupart du temps des bouleversements significatifs dans les méthodes et la culture d'une organisation.
Ces changements sont d'autant plus complexes à accompagner qu'ils font appel à des concepts qui peuvent sembler contre-intuitifs.
Par exemple, pour reprendre l'idée du paragraphe précédent, "perdre" du temps à faire davantage de changements de série va nous permettre de livrer le client plus rapidement. Ou encore le fait qu'il ne faut pas viser un "TRS" (Taux de Rendement Synthétique, une mesure de la performance opérationnelle d'un équipement) élevé pour mieux répondre aux besoins des clients.
Ces aspects nécessitent de ne pas négliger les besoins en formations pratiques pour toutes les personnes impliquées, ainsi qu'un fort accompagnement sur le terrain au démarrage.
4) Tous les flux ne se prêtent pas facilement au flux tiré
Enfin, certains processus sont de nature particulièrement compliqués à passer à ce type de flux.
On peut citer par exemple les industries qui transforment leurs matières premières dans des fours comme la sidérurgie ou la verrerie : ces outils de production ne sont pas facilement adaptables à une cadence de production qui serait dictée par la demande en aval.
Ou encore l'agroalimentaire qui est souvent conditionné par ce qui est produit en amont par l'agriculture.
Comment mettre en place le flux tiré ?
En fonction de l'entreprise concernée, notamment de sa taille et de son domaine d'activité, sa mise en place peut-être une démarche relativement conséquente.
La première condition avant de se lancer reste donc, comme pour toute démarche Lean, un engagement et un mandat donné par la Direction de l'entreprise. Sans ce prérequis, il est inutile de se lancer.
La mise en place de ce process doit être envisagée comme un projet à part entière, et nécessite donc d'être structurée.
Découvrez ici le cycle de vie de gestion d'un projet.
Voici les principales étapes à suivre :
- Cadrage du projet
- Analyse de l'existant
- Définition de la cible
- Création du nouveau flux
- Simulation et test
- Présentation des outils de gestion de flux sur terrain
- Formation
- Lancement
1) Cadrage du projet
Le cadrage de projet se fait en définissant notamment le périmètre, les objectifs à atteindre et l'équipe projet.
Le périmètre peut être l'ensemble du flux de production de l'entreprise, ou simplement une partie des lignes de production.
Parfois le projet peut inclure plusieurs sites de production connectés entre eux et intégrer des fournisseurs dans la démarche.
2) Analyse de l'existant
Il s'agit ici de faire une analyse VSM du ou des flux concerné(s).
Rappelons qu'une VSM permet de représenter un processus dans le but de distinguer les étapes qui représentent une valeur ajoutée pour le Client, de celles qui n'en apportent pas.
Si tous les éléments traversant ce flux ne passent pas systématiquement par les mêmes opérations, par exemple pour une fabrication de pièces métalliques, si certaines sont mises en peinture et d'autres pas, il est important de compléter la VSM par la construction d'une matrice produits / process.
Une matrice produits / process est un tableau listant chacun des types de produits qu'il est possible de fabriquer sur ce flux.
Chaque colonne du tableau correspond à une étape du process du flux (par exemple, la mise en peinture).
Et chaque case du tableau est cochée ou non selon qu'un type de produit passe ou pas par l'étape correspondante du processus.
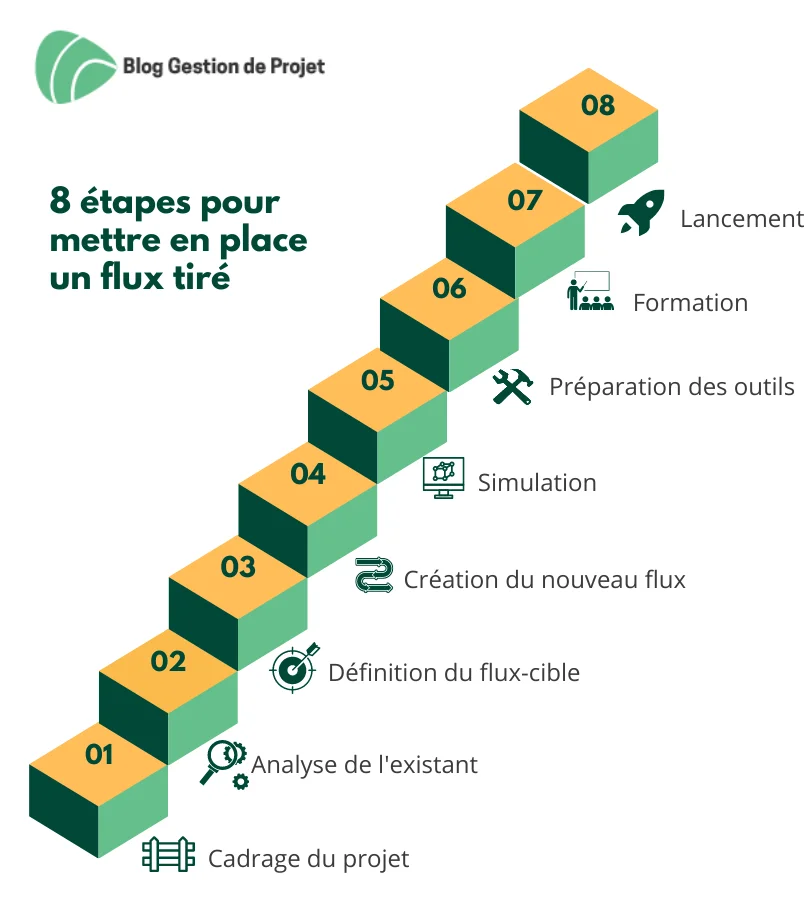
3) Définition du flux "cible"
Ici, on va construire la VSM-cible.
Rappelons qu'une cartographie VSM va tenter d'analyser d'abord l'existant pour ensuite faire une cartographie de l'état futur désiré.
Pour cela, on représente le flux « cible », fictif pour le moment, mais qui intègre les simplifications que l'entreprise prévoit de réaliser.
Ainsi, selon les modifications à apporter au flux qui sont identifiées entre la VSM initiale et la VSM-cible, on va créer des sous-projets ou des sous-groupes de travail pour traiter chaque sujet.
Par exemple, un sous-groupe pourra travailler spécifiquement sur le flux du contrôle qualité.
Un autre sous-groupe pourra travailler sur la réduction des temps de changement de série (SMED) sur un des postes de production, etc.
4) Création du nouveau flux
Le flux tiré à mettre en place peut être décrit à l'aide d'un schéma global des flux.
Une première version des standards de fonctionnement du flux est construite à cette étape.
5) Simulation
Cette étape est d'autant plus importante que le périmètre du projet est vaste et complexe.
L'objectif de la simulation est de tester "à blanc" le mode de fonctionnement proposé à l'étape précédente afin de l'améliorer avant de le transposer sur le terrain.
Pour cela, on bâtit des maquettes des différentes étapes du flux et on construit des scénarios de production basés sur des historiques, les plus proches possibles de la réalité, donc idéalement incluant des aléas de production tels que des pannes.
On simule un certain nombre de cycles de production. On observe le résultat et on en tire des conclusions qui vont permettre d'améliorer les standards de fonctionnement proposés initialement et de créer des standards de réaction adaptés qui serviront lors de la survenue des aléas.
6) Préparation des outils de gestion du flux sur le terrain
Une fois que la simulation est proche de l'aboutissement, les outils de gestion du flux prévu par les standards sont transposés et implantés sur le terrain.
7) Formation
La formation de l'ensemble des acteurs concernés par les changements est primordiale.
Cette formation doit être la plus concrète possible afin d'aider à comprendre les notions parfois contre-intuitives qui contribuent au flux tiré.
Les outils de simulation utilisés à l'étape 5 peuvent constituer une base intéressante pour une formation la plus pratique possible.
8) Lancement
C'est la mise en œuvre réelle sur le terrain, avec l'application de l'ensemble des standards qui ont été définis et l'utilisation des outils qui ont été créés.
Une forte mobilisation de l'équipe projet reste indispensable pendant un certain temps pour accompagner les acteurs du flux, identifier les difficultés qui n'avaient pas pu être anticipées, et proposer des améliorations adaptées de façon réactive.
Comme dans tout projet, la communication tout au long de la démarche, du lancement jusqu'à la mise en œuvre, est fondamentale afin de préparer les équipes au changement.
Des outils pratiques
La mise en place des flux tirés fait appel à un certain nombre d'outils du domaine du Lean et de la Supply Chain.
Il n'est pas possible ici de donner une description détaillée de chacun de ces outils, mais certains pourront faire l'objet de prochains articles sur le blog.
Voici les principaux outils qui peuvent être utilisés :
1) La VSM
La Value stream mapping dont nous avons déjà parlé précédemment, pour l'analyse du flux.
2) La matrice produits / process
Également évoquée à l'étape 2 du processus décrit ci-dessus. Elle permet de comprendre quelles sont les étapes de production des différentes catégories de produits fabriqués par l'entreprise.
3) Le S&OP (Sales and Operations Planning)
Le S&OP (Sales and Operations Planning) ou PIC en français (Plan Industriel et Commercial) est une négociation régulière entre les services commerciaux et les équipes chargées des opérations / production, afin d'aligner les demandes des clients avec la capacité opérationnelle de l'entreprise.
C'est le S&OP qui définit le rythme de production et le mix produits de chaque période.
4) La boite de nivellement
La boîte de nivellement, également appelée Heijunka ou séquenceur est un outil qui permet de lisser la production, c'est-à-dire "faire un peu de tout, tout le temps", en fonction de la demande client.
Elle contribue à offrir des délais compétitifs aux clients et va servir à réguler le mix produits.
5) Le Kanban, ou lanceur
Le Kanban est un outil visuel permettant à un poste de travail "aval" de faire déclencher les opérations du poste de travail "amont" en fonction des besoins et dans l'ordre des besoins.
6) Le SMED
Déjà évoqué plus haut. Il s'agit d'une méthode d'analyse permettant de réduire le temps nécessaire à un changement de série, ou changement de type de fabrication, sur un équipement de production donné.
7) Le Just-In-Time (JIT)
Le Just-In-Time (JIT) ou Juste-A-Temps (JAT) en français, est une méthode qui tend à aller vers l'idéal du flux tendu en supprimant tout stock intermédiaire. C'est un des piliers de la Maison du Lean illustrée plus haut.
8) Le Stock tampon, supermarché, ou poumon
Pour les flux qui comportent encore une variabilité importante et/ou qui connaissent régulièrement des aléas, l'idéal du flux tendu et du "zéro stock" peut être trop ambitieux dans un premier temps.
Dans ce cas, le flux tiré peut prévoir des stocks tampons intermédiaires entre deux étapes du processus de production pour amortir l'effet de ces aléas.
Mais contrairement aux stocks subis du flux poussé, le stock tampon du flux tiré est dimensionné avec une limite. Lorsque cette limite est atteinte, la production en amont doit s'arrêter.
Conclusion
Le flux tiré est un outil puissant du Lean.
Comme expliqué dans l'article, il permet de renforcer l'orientation client d'une organisation en organisant ses processus de fabrication ou de prestation de service au rythme de la demande des clients.
Sa mise en place peut être une démarche assez longue et complexe, et constituer une révolution culturelle importante dans certaines organisations.
Mais le retour sur investissement d'un projet bien mené et bien accompagné est significatif à la fois en matière de qualité, coûts et délais.
De prochains articles sur le blog approfondissent certains aspects de ce concept.
Satisfait mais j’aimerais connaître un peu plus sur les domaines de la logistique
Merci pour votre intérêt.
Nous avons des articles liés plus à la chaine de production (Lean management et Lean Manufacturing), comme :
La chaine d’approvisionnement.
La méthode du Just-à-temps.
Le taux de rendement synthétique (TRS) qui sert à évaluer l’efficacité des équipements industriels.
L’ordonnancement et la planification de la production.