Beaucoup parmi nous le savent : la conduite du changement peut être l'un des challenges les plus importants lors du déploiement d'un projet.
Il ne sera donc pas surprenant de se dire que la mise en place d'une démarche Lean dans une organisation nécessite elle aussi un accompagnement.
D'ailleurs, plutôt que de conduite du changement, c'est bien d'accompagnement au changement puisque ce sont nos équipes qu'il s'agit d'accompagner.
Dans cet article, nous allons parcourir les différentes étapes du changement dans un contexte de transformation Lean.
Qu'est ce qu'une démarche Lean ?
Une démarche Lean est une réflexion structurée qui conduit une entreprise vers une logique d'amélioration continue centrée sur la valeur ajoutée créée pour le Client.
Cette démarche va se traduire par une feuille de route qui va guider toutes les actions d'amélioration continue menées dans l'organisation.
Découvrez ici comment construire une feuille de route Lean en 3 étapes.
Qu'est ce que l'accompagnement au changement ?
L'accompagnement au changement est l’ensemble des méthodes et moyens mis en œuvre pour accompagner un projet changement, en l'occurrence une transformation Lean, dans le but de favoriser l'adhésion par l'ensemble des collaborateurs à la nouvelle situation.
Cette démarche repose sur une approche concertée et coconstruite, dans le but de limiter les résistances au changement éventuelles.
En savoir plus sur l'accompagnement au changement.
Les 5 étapes d'accompagnement au changement Lean
Afin de réussir à déployer une culture Lean dans une organisation, voici les principales étapes du changement à traverser :
- Comprendre les perceptions
- Remettre en cause les modes de pensée
- Adapter les comportements
- Créer des habitudes
- Mettre en place la culture
1) Comprendre les perceptions
Nous allons évoquer ici la façon dont nous percevons les choses qui nous entourent.
Que voyez-vous sur l'image suivante ? :
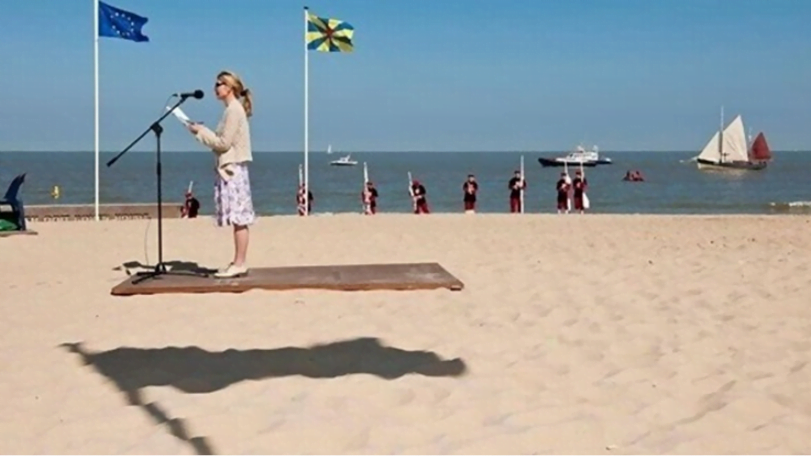
Un tapis volant ?
Non, bien sûr. C'est une impression causée par l'ombre d'un drapeau que notre cerveau assimile à tort à l'ombre de l'estrade.
Comment s'explique ce mécanisme ?
Il est dû au fait que notre cerveau est par défaut très paresseux.
Et la plupart du temps c'est une "qualité" qui nous arrange bien.
Cela signifie que notre cerveau va économiser de l'énergie pour traiter en "mode automatique" toutes les situations qui lui semblent familières, sans avoir besoin de les analyser en détails.
Par exemple, lorsqu'une personne expérimentée conduit une voiture avec une boîte de vitesses manuelle, elle n'a pas besoin de réfléchir ou de regarder le levier de vitesse au moment du démarrage pour passer la première vitesse, puis la deuxième.
D'une manière plus générale, quand nous effectuons un trajet en voiture quotidiennement, nous n'avons plus non plus besoin de réfléchir à l'itinéraire pour savoir quelle direction prendre à chaque carrefour.
Nous agissons presque instinctivement.
Quels sont les pièges de ce mécanisme ?
Là où par contre cette caractéristique de notre cerveau à reconnaître des situations familières et à agir instinctivement va nous jouer des tours, c'est lorsqu'un léger détail va être différent par rapport aux situations auxquelles nous sommes habituées.
Restons par exemple dans le cas d'un trajet en voiture :
Nous prenons la même direction que notre trajet quotidien habituel, mais exceptionnellement nous devons aller à un rendez-vous situé légèrement hors de ce trajet.
Dans ce cas, il peut nous arriver de manquer la sortie si nous ne sommes pas concentrés car notre cerveau va nous guider sur notre itinéraire habituel.
C'est ce même mécanisme qui explique le fonctionnement des illusions d'optique.
Dans la vie de tous les jours, notre cerveau est habitué à voir certains objets, certaines formes, des choses organisées d'une manière logique.
Si on lui présente une image inattendue, il va la confondre avec une construction, des formes, qui lui sont plus familières.
Quel est le lien avec une démarche Lean ?
Une des complexités pour accompagner au changement réside dans cette difficulté naturelle que nous avons à détecter les choses qui sont un peu différentes de ce dont nous avons l'habitude.
Dans le cadre d'une démarche Lean, cela amène à nier la nécessité de remettre en cause nos modes de fonctionnement et nos habitudes de travail.
Au niveau des stratégies d'entreprises, plusieurs exemples existent de sociétés qui ont manqué le "train" de certaines évolutions majeures.
Comme exemple : des entreprises leaders dans le domaine de la photographie qui ne se sont pas adaptées assez rapidement au virage du numérique qu'elle n'avaient pas vu venir.
Ou dans les activités quotidiennes, il n'est pas rare face à un problème, par exemple technique, d'entendre un expert dire "ah, je sais ce qu'il s'est passé, on a eu la même chose il y a deux ans, c'est la pompe qui a dû lâcher". Alors qu'en fait il s'agit d'un raccourci qui est parfois faux.
Même si cet expert cherche de bonne foi à aider et à faire gagner du temps, cette attitude empêche souvent de voir les vrais problèmes et de travailler dessus dans une démarche d'amélioration continue.
L'anecdote la plus parlante pour illustrer les comportements liés à la résistance au changement est "Qui a piqué mon fromage ?".
2) Remettre en cause les modes de pensée
Le fait d'être conscient de ces mécanismes de perception va pouvoir aider à partager dans l'organisation ou l'entreprise des modes de pensée qui seront nécessaires pour le bon déploiement d'une démarche Lean.
Il y a trois modes de pensée principaux qui sont adaptés pour le Lean :
- L'amélioration permanente
- La simplification
- Le Gemba
2.1) L'amélioration permanente
L'être humain a naturellement tendance à chercher à atteindre une perfection ultime qui n'existe pas.
Il est souvent plus confortable de penser "nous avons été très efficaces, nous avons trouvé une superbe innovation il y a 5 ans, maintenant nous sommes leaders, cela signifie donc qu'il nous suffit de continuer à travailler de la même façon pour rester compétitifs".
Malheureusement… ou heureusement, c'est faux ! Les autres entreprises vont continuer à progresser et l'entreprise qui est compétitive à un moment donné ne pourra pas le rester si elle ne continue pas dans un esprit d'amélioration continue.
En pratique, c'est souvent une contrainte ou une nécessité forte qui va permettre de stimuler l'innovation et d'accélérer le changement. Par exemple, lorsque la question de la survie de l'entreprise est en jeu.
Ainsi, Toyota, qui fait figure aujourd'hui de leader dans la mise en oeuvre d'une démarche Lean, s'est différencié par rapport à ses concurrents dans les années 1950, lorsque sa situation économique dans le Japon d'après-guerre était très précaire.
Les changements drastiques mis en oeuvre à ce moment là répondaient à une question de survie de l'entreprise.
Le frein est lié au sentiment de risque qui est associé avec le changement. En situation de survie, la motivation, la nécessité, vont dépasser ce sentiment de risque.
Mais idéalement, une entreprise doit être consciente de la nécessité de s'adapter en permanence.
En réalité, il y a plus de risques à rester comme on est qu'à changer.
Cela se reflète bien d'ailleurs dans l'histoire "qui a piqué mon fromage ?" évoquée au chapitre précédent.
2.2) La simplification
En France, il faut actuellement plus d'un mois pour renouveler son passeport.
Pour faire changer une pièce défectueuse sur un petit appareil d'électroménager, il faut le déposer en magasin et attendre plusieurs jours pour récupérer son bien.
Dans plusieurs pays d'Europe, l'enchaînement des rendez-vous avec différents spécialistes pour se faire diagnostiquer certaines maladies prend plusieurs semaines également.
Faut-il réellement plus de quelques heures pour contrôler, saisir et imprimer un passeport, pour ouvrir un appareil et remplacer une pièce, et pour réaliser et analyser plusieurs imageries médicales ?
Evidemment non. Mais ce temps qui s'écoule entre l'expression de notre besoin et la réalisation de la fabrication ou du service demandé est principalement composé de "non-valeur ajoutée".
Il peut s'agir par exemple d'attente entre la succession de deux opérations, ou encore de la réalisation d'opérations ou de contrôles inutiles par rapport à la finalité attendue.
Toutes ces opérations sont pénalisantes pour le client, qui peut parfois, s'il en a la possibilité, s'adresser à un autre fournisseur ou prestataire pour répondre à sa demande dans de meilleurs délais.
Ce sont ici des exemples de ce qui peut être amélioré par la réalisation de chantiers d'amélioration Lean.
Il existe de nombreuses façons d'analyser les processus pour identifier la "valeur ajoutée" et la "non-valeur ajoutée".
Ces analyses permettront d'identifier de nombreuses sources de simplification des processus sur lesquelles il sera plus ou moins facile d'intervenir.
C'est cette rechercher continue de la simplication des processus qui constitue le deuxième mode de pensée fondamental qui doit animer une entreprise Lean.
2.3) Le Gemba
Gemba, ou Genba, en japonais, peut se traduire approximativement par "le terrain" ou "là où se passe l'action".
Ce terme est très important dans une culture Lean.
Il évoque le fait que la valeur ajoutée produite par une entreprise ou une organisation est réalisée sur le terrain, par les personnes qui sont généralement à la base de la pyramide hiérarchique.
Ce sont elles qui transforment le produit ou mettent en oeuvre le service fourni au Client.
C'est leur travail qui a une conséquence directe sur la qualité de ce qui va être délivré.
Ce sont ces personnes qui ont la meilleure connaissance de la réalité du terrain, qui y passent 7 à 8 heures par jour, et qui sont les mieux placées pour identifier les sources d'amélioration.
On parle parfois du principe de pyramide inversée :
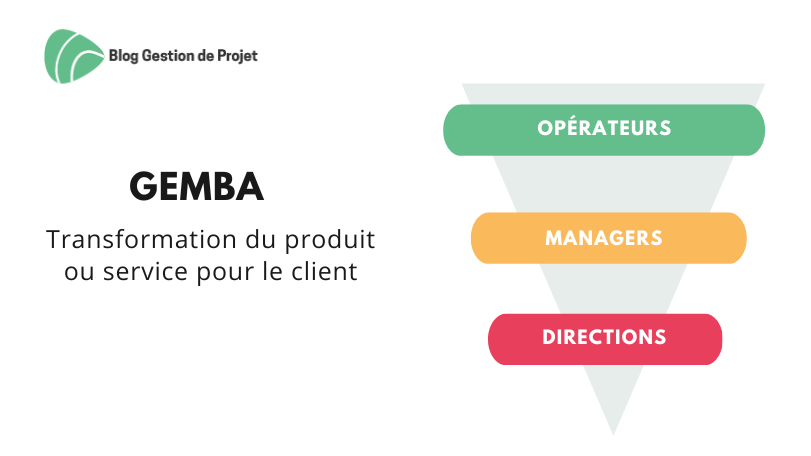
Il s'agit ici de prendre conscience que ce ne sont pas les diplômes ou la position hiérarchique qui vont définir quelles sont les personnes les mieux placées pour mettre en oeuvre le changement et la transformation Lean.
Les équipes terrain doivent être nécessairement impliquées.
D'une part parce que, comme décrit plus haut, ce sont elles qui vivent au quotidien les vrais problèmes et qui seront en mesure de proposer les solutions les plus pragmatiques.
Et d'autre part parce qu'il sera important qu'elles s'approprient les changements afin d'être motrices dans leur mise en oeuvre.
Le Management, lui, aura un rôle de facilitateurs et de support vis à vis des équipes terrain.
3) Adapter les comportements
Une fois que ces modes de pensée sont partagés par la majorité de l'organisation, progressivement, des nouveaux comportements seront générés.
Les principaux comportements qui vont accompagner le déploiement d'une culture Lean sont :
- la mise en oeuvre du changement
- l'orientation Client
- et le "bon du premier coup"
Voyons plus en détails comment ces comportements peuvent naître des nouveaux modes de pensée et comment ils s'inscrivent dans une culture Lean.
3.1) La mise en œuvre du changement
Comme nous l'avons vu plus haut, la recherche de l'amélioration permanente nécessite d'accepter de remettre en cause régulièrement nos méthodes de travail.
Et pour le faire de la meilleure façon qui soit en impliquant les personnes concernées, il convient de construire ces changements sur le Gemba.
Généralement on distingue 4 types de démarches d'amélioration qui se répètent en cycles :
- Une démarche de standardisation permet de diminuer la variabilité d'un processus et d'améliorer la qualité de ce qu'il produit
- Un chantier Lean permet d'améliorer de manière significative la valeur de ce processus
- Une rupture technologique passant par un investissement est parfois également nécessaire
- Et suite à la mise en place d'un chantier Lean et/ou d'une rupture technologique, une phase intensive de résolution de problèmes permettra de traiter les principales causes de variabilité, avant qu'une nouvelle démarche de standardisation ne porte ses fruits.
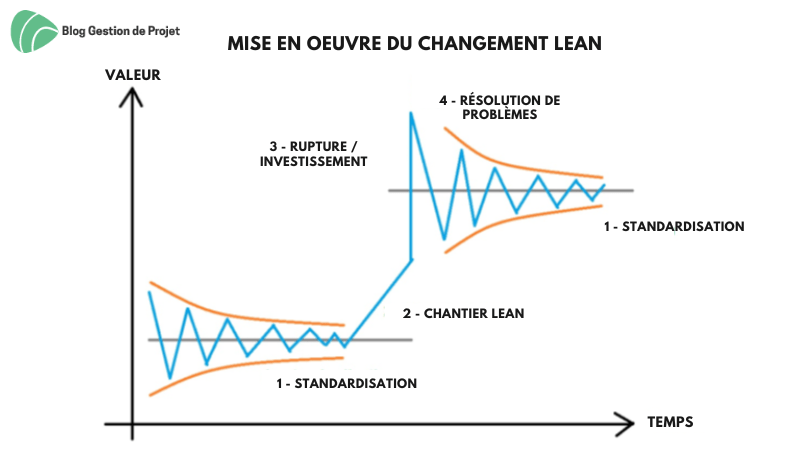
Pour la résolution de problèmes, en fonction des enjeux, on pourra aller d'une simple analyse "5 pourquoi" ou "arbre des causes" jusqu'à un projet 6 sigma, en passant par l'utilisation d'autres outils tels que par exemple la méthode Ishikawa ou "5 M".
Modèle du diagramme Ishikawa
Identifiez les vrais problèmes à l'aide de la méthode Ishikawa, avec 4 études de cas
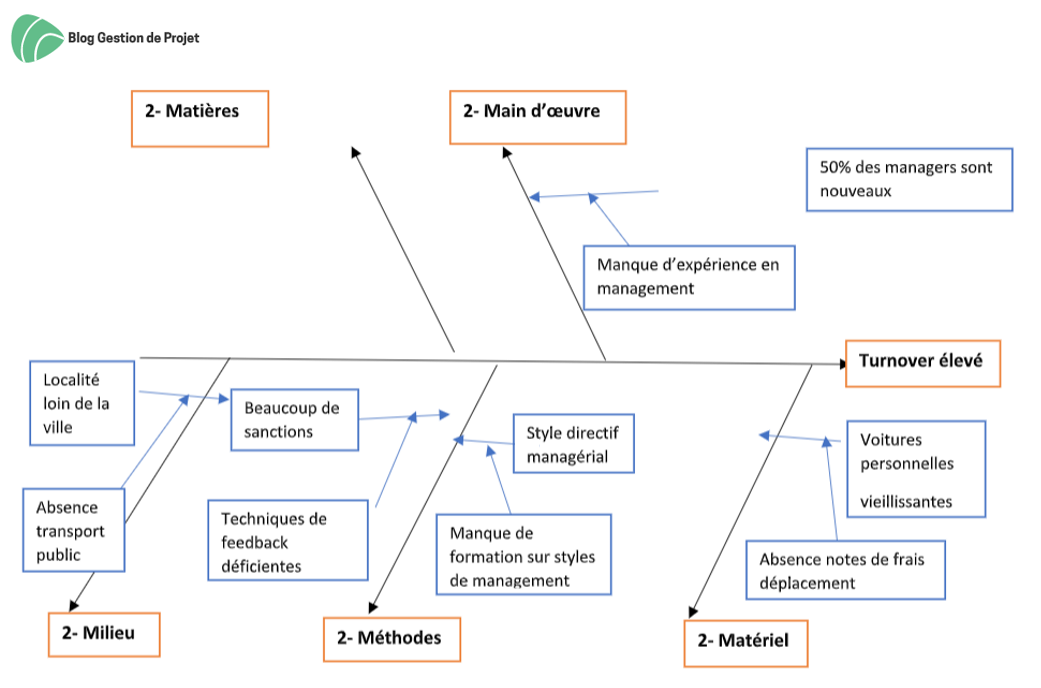
3.2) L'orientation Client
L'orientation Client va se trouver à la croisée de l'amélioration permanente et de la simplification.
En effet, la viabilité d'une entreprise ou d'une organisation passe par la satisfaction des Clients (qu'il s'agisse de leur propose un produit ou un service).
La réponse aux attentes des Clients doit donc être la principale boussole de l'amélioration de nos processus.
Cela passe par les étapes suivantes :
- Un travail avec le Client pour identifier ses besoins explicites et implicites
- Un diagnostic des processus de l'entreprise avec des outils tels que la VSM qui mettront en évidence les étapes qui contribuent aux attentes du Client et les étapes qui n'ont au contraire pas de valeur ajoutée
- La suppression autant que possible des étapes qui n'apportent pas de valeur ajoutée (simplification), ce qui permet de diminuer les coûts ainsi que les risques de génération de problèmes/défauts dans le processus
- L'adaptation du processus pour répondre au mieux aux attentes du Client (amélioration permanente).
Cette démarche va générer une amélioration de la qualité, ainsi qu'une baisse des coûts et des délais.
3.3) Le "bon du premier coup"
La mise en place de la simplification sur le terrain (Gemba) doit nous inciter à considérer chaque défaut généré au cours d'un processus comme tout simplement inacceptable.
Ces modes de pensées vont ainsi induire les comportements suivants :
- Mettre en place une détection immédiate des défauts à l'étape où ils risquent d'être générés
- Ne pas transmettre de défaut à une étape suivante du processus
- Dès qu'il y a une suspicion de défaut, l'isoler, stopper le processus de production si c'est nécessaire, puis rebuter ou retraiter en dehors du processus le produit isolé.
A l'inverse, les comportements ci-dessous sont à bannir :
- Remettre à plus tard le traitement et/ou l'analyse d'un défaut
- Espérer qu'un défaut produit à un endroit du processus soit corrigé lors d'une étape suivante
- Au niveau du contrôle qualité, tout miser sur un contrôle final exhaustif très consommateur de ressources
- Ou, encore pire, accepter que des produits ou services non conformes arrivent chez le Client.
4) Créer des habitudes
Dans ce domaine du changement, nous sommes bien évidemment en lien avec tout ce qui touche le comportement humain.
Ainsi, pour pérenniser le changement et créer les habitudes, il va être nécessaire de rassembler les trois "ingrédients" suivants :
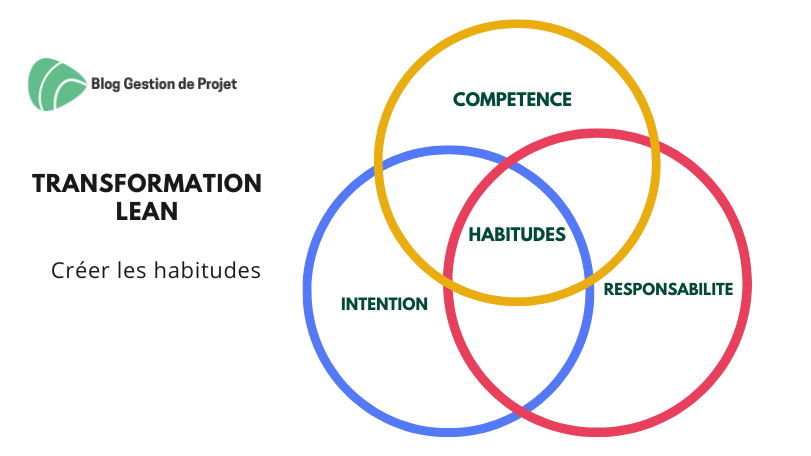
4.1) La compétence : le fait de pouvoir faire ce qui est attendu
Ceci peut être développé auprès de nos collaborateurs par la formation, l'acquisition d'expérience, ainsi que le suivi précis des compétences et leur adéquation aux besoins.
4.2) L'intention : le fait d'avoir la volonté de réaliser ce qui est demandé
Il s'agit ici de la motivation des collaborateurs.
Elle passe déjà par la prise en compte lors des recrutements de l'adéquation entre les aspirations de la personne et les missions du poste.
Elle se cultive ensuite en donnant du sens à ce qui est demandé et en communiquant sur la finalité des choses auprès de nos équipes.
4.3) La responsabilité : le fait d'avoir la mission de réaliser l'activité attendue
Il s'agit là de clarifier les responsabilités de chacun à travers des outils comme les fiches de mission ou encore le RACI (définir qui est responsable de la réalisation d'une action (R), qui est garant et doit rendre des comptes (A), qui contribue (C) et qui doit être informé (I)).
Modèle de la matrice RACI
Matrice RACI sur Excel avec une étude de cas concrète
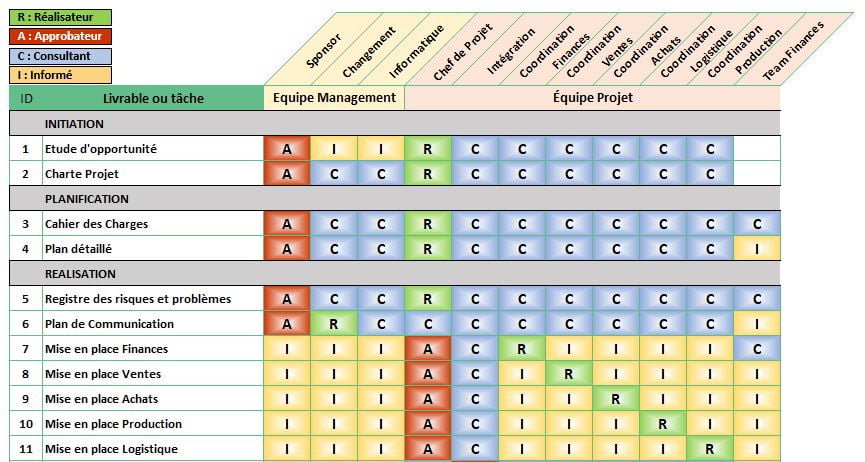
Revenons sur le point concernant l'acquisition des compétences.
Nous parlons ici de Lean, qui est une démarche long-terme, et de pérennisation du changement.
Cela nécessite de se donner du temps d'apprentissage et de laisser le droit à l'erreur, tout en mettant sous contrôle ce risque d'erreur par les personnes qui sont en cours de formation.
Pour atteindre une pleine maîtrise des habitues, il est considéré que l'apprentissage va passer par 4 phases successives :
- "Inconsciemment incompétent" : face à quelque chose de nouveau sur quoi nous n'avons aucune connaissance, nous ne pouvons pas dans un premier temps appréhender correctement sa complexité. Nous aurons donc tendance à sous-estimer les difficultés. Par exemple lorsque enfant nous montons pour la première fois sur un vélo après avoir vu nos parents en faire sans difficulté, nous imaginons que nous allons pouvoir maîtriser sa conduite immédiatement. En pratique, nous allons certainement tomber lors de notre premier essai.
- "Consciemment incompétent" : suite à cette expérience, nous prenons conscience des difficultés. Nous allons donc être plus prudent et demander de l'aide (par exemple des roulettes à l'arrière du vélo) et des conseils pour progresser en maîtrise.
- "Consciemment compétent" : à force de pratique, nous allons finir par réussir à réaliser l'action demandée. Mais dans un premier temps, cela va exiger que nous conservions une concentration constante pour bien maîtriser tous les aspects de la compétence.
- "Inconsciemment compétent" : enfin, lorsque nous aurons répété une opération et des gestes de multiples fois, nous serons capables de les réaliser de manière "instinctive" sans avoir à nous concentrer particulièrement sur ce que nous sommes en train de réaliser.
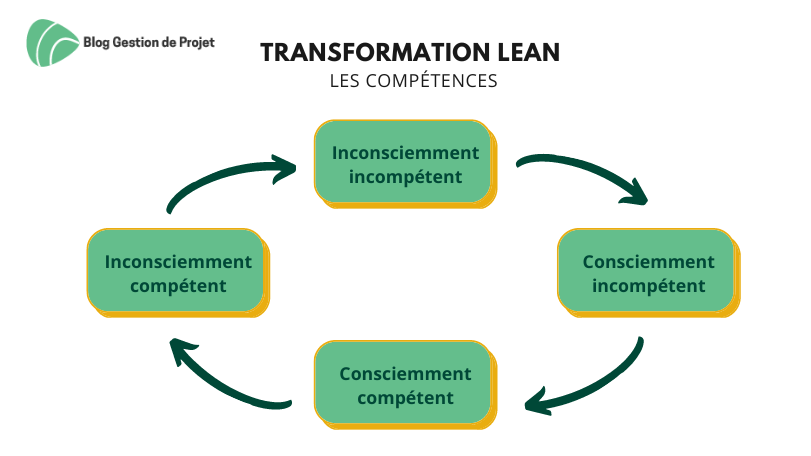
Ce sont ces différents éléments qui contribuent à développer les nouvelles habitudes.
5) Mettre en place la culture
Ces habitudes en cours de développement vont servir de socle pour commencer à bâtir la culture Lean de l'entreprise.
La culture est un ensemble d'habitudes partagées par l'ensemble des personnes d'une organisation.
Pour fédérer tout un groupe et déployer cette culture, il sera nécessaire de :
- Donner un cap, notamment avec la feuille de route établie dans le cadre de la démarche Lean
- Créer des rituels pour piloter le progrès et instaurer un rythme pour le déroulement de la feuille de route et des chantiers d'amélioration qui en découlent.
Le diagramme de Nemoto ci-dessous permet de visualiser les rôles de chacun en fonction de leur place dans l'organisation :
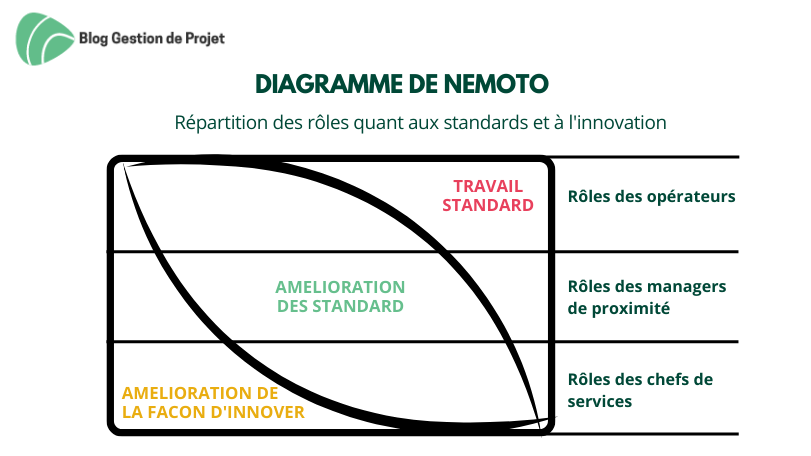
- Les opérateurs, durant leurs journées de travail, vont principalement appliquer le travail standard. Mais il est important de leur permettre également de partager leurs idées d'amélioration des standards existants
- Les managers de proximité vont eux consacrer davantage de temps à la résolution de problèmes et à l'amélioration de standards (en s'appuyant notamment sur l'observation et les idées de leurs collaborateurs)
- Les chefs de services quant à eux auront une vision plus globale du fonctionnement de l'organisation et joueront un rôle dans la réflexion sur l'innovation et le pilotage de l'amélioration continue.
Conclusion
Nous avons vu dans de précédents articles les étapes importantes pour la mise en place d'une démarche Lean.
C'est une démarche qui n'est pas anodine, qui demande un engagement de la Direction et une mobilisation de l'ensemble de l'organisation.
Les principaux freins rencontrés dans le lancement d'une telle démarche sont humains et c'est normal.
Nous ne sommes pas naturellement conditionnés pour être à l'aise avec le changement, même si bien sûr d'une personne à une autre, certains seront davantage moteurs dans le changement.
Le changement s'accompagne donc, et il est important de passer par les différentes phases de montée en maturité décrites dans cet article pour ancrer les habitudes et développer une réelle culture d'entreprise.
Par opposition, la "marche forcée" pourra apporter certains résultats à court-terme, mais qui ne perdureront pas.
La tâche du Management ici est de trouver le subtil équilibre entre impulser une bonne dynamique de transformation Lean et laisser le temps aux collaborateurs de prendre conscience de l'intérêt et de la finalité de ces changements.