Sur un site industriel, l'adoption d'une démarche Lean implique la mise en place du Lean Manufacturing, qui englobe tous les outils et concepts Lean liés à un environnement de production.
Le Lean Manufacturing met en avant la nécessité du bon fonctionnement des équipements industriels.
Pour une évaluation approfondie de cette performance, on utile l'outil du Taux de Rendement Synthétique, également connu sous l'acronyme TRS.
Cet article examine d'abord la définition et le calcul du TRS.
Ensuite, il explore comment le TRS contribue à l'amélioration continue des équipements de production.
Enfin, il remet en question l'utilisation traditionnelle du TRS dans l'industrie.
Définition TRS
Intéressons-nous tout d'abord à ce que représente le TRS dans le cadre de la démarche lean et à la façon dont il est calculé.
Le TRS est un ratio qui s'exprime sous forme de pourcentage, compris entre 0 et 100 %.
A noter que, selon les valeurs de référence prises en compte pour le maximum théorique, il pourrait dans certains cas être possible de dépasser les 100 %.
Méthode de calcul
Le Taux de Rendement Synthétique (TRS) est calculé en évaluant le rapport entre le nombre de pièces bonnes réellement produites durant une période donnée et le nombre maximal de pièces qui auraient pu être fabriquées dans des conditions idéales, conformément aux standards Lean.
Ainsi, la formule pour déterminer le TRS est :
sur la période considérée
Il en résulte que le TRS est un ratio qui peut évoluer dans le temps, à la hausse comme à la baisse.
Il peut se calculer soit pour un équipement de production pris isolément, soit pour une ligne de production.
Exemple :
Sur ma journée de lundi, j'ai fabriqué 2 113 pièces bonnes. Mon équipement fonctionne 24 heures par jour et il est capable de fabriquer 105 pièces par heure.
Mon TRS est donc de :
= 83,8 %
Les 3 composantes du TRS
Voyons à présent comment il est possible d'aller plus en détails dans l'analyse du TRS en s'appuyant sur ses 3 composantes :
La disponibilité, la performance et la qualité.
2.1) Disponibilité
La disponibilité d'un équipement ou d'une ligne de production représente le temps réel de bon fonctionnement rapporté au temps d'ouverture, c'est-à-dire le temps durant lequel le site avait décidé de produire.
Les différents éléments qui peuvent expliquer la différence entre le temps d'ouverture et le temps réel de bon fonctionnement sont :
- Les pannes
- Une rupture de matières premières
- Un manque de personnel
- Les arrêts programmés (maintenance préventive, …)
- Les temps de changement de série entre 2 productions
La disponibilité s'exprime sous forme d'un ratio compris entre 0 et 100 %.
Exemple :
Mon site de production fonctionne 24 heures / 24.
Sur ma journée de lundi, j'ai eu 2 heures de pannes et 1/2 heure de temps de changement de série.
Mon taux de disponibilité pour la journée de lundi est donc de :
= 89,6 %
2.2) Performance
La performance d'un équipement ou d'une ligne de production s'exprime également comme un ratio en pourcentage.
Elle représente la vitesse à laquelle les pièces sont produites, par rapport à la vitesse nominale de l'installation.
La différence entre ces dernières provient principalement des pertes de cadence, mais on comptabilise dans ce ratio également les pertes dues aux micro-arrêts (arrêts de type disjonctions et réarmement).
C'est la seule composante qui, en théorie, pourrait dépasser les 100 % : cela signifierait que l'on a poussé l'équipement au-delà de sa vitesse nominale.
Mais tout dépend de la référence que l'on décide de prendre pour la vitesse nominale.
A noter que la vitesse nominale prise en compte peut également varier en fonction du type de pièces qui sont fabriquées.
En effet, d'un type de fabrication à un autre, le temps de cycle d’un équipement pour fabriquer une pièce peut être très différent.
Exemple :
Pour ma production de lundi, ma cadence de machine était réglé à 100 pièces par heure. Or pour ce type de fabrication, la cadence nominale est de 105 pièces par heure.
Mon taux de performance durant cette journée est donc de :
= 95,2 %
2.3) Qualité
La composante qualité du TRS représente le rapport entre le nombre de pièces bonnes et le nombre total de pièces fabriquées sur une période donnée.
L'écart entre ces dernières peut correspondre à :
- Des pièces défectueuses à rebuter
- Des pièces à remanier pour les remettre en conformité
- Des pièces d'essai destinées au réglage de l'équipement durant le lancement de fabrication.
La composante qualité est encore une fois un ratio qui peut varier entre 0 et 100 %.
Exemple :
Sur ma journée de lundi j'ai fabriqué un total de 2 150 pièces.
Sur ces 2 150 pièces, 37 étaient non-conformes.
Mon taux de qualité pour cette journée est donc de :
= 98,3 %
2.4) Calcul du TRS à partir des 3 composantes
Les 3 composantes que je viens de décrire rassemblent toutes les causes d'écart possibles entre le nombre de pièces bonnes fabriquées et le nombre de pièces maximum théorique que l'on aurait pu fabriquer durant la même période.
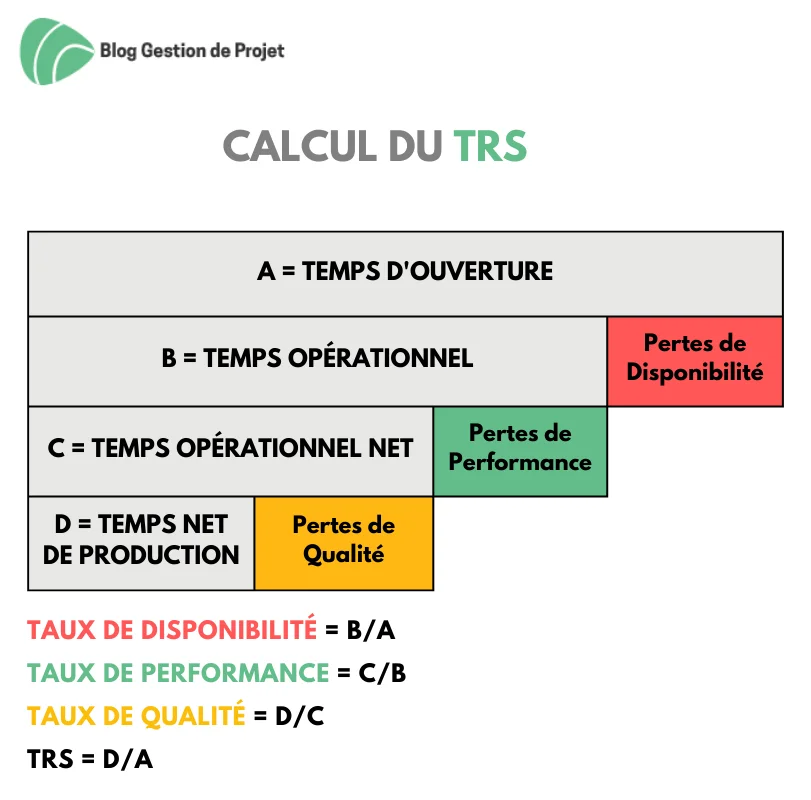
Il est donc possible de reconstituer le TRS par le produit de ces 3 taux :
TRS = taux de disponibilité x taux de performance x taux de qualité
Soit dans le cas de nos exemples ci-dessus :
= 83,8 %
Nous retrouvons bien le même résultat trouvé par la méthode globale :
TRS = nombre de pièces bonnes fabriquées / nombre de pièces maximum théorique sur une période donnée.
Voyons à présent comment nous pouvons exploiter ces indicateurs afin de mettre en place des axes d'amélioration.
Amélioration continue grâce au TRS
Puisque les 3 composantes du TRS regroupent l'ensemble causes de pertes de production possibles liées à des équipements, nous pourrons nous en servir afin d'identifier les actions d'amélioration les plus pertinentes.
1) Axe "disponibilité"
Nous avons vu que la disponibilité est impactée par les temps d'arrêts des équipements de production.
Voici les principales démarches qui vont permettre de réduire ces temps d'arrêts et donc d'améliorer le taux de disponibilité :
- La TPM (Total Productive Maintenance) : Est un ensemble de concepts très complet qui vise à maximiser l'efficacité globale des équipements. Elle permet notamment d'attaquer les problèmes de pannes. C'est une démarche d'horizon moyen/long-terme qui s'étend au moins sur plusieurs mois
- Le SMED (Single Minute Exchange of Die) : Est une démarche qui vise à réduire les temps de changement de série entre deux productions de types de pièces différents
- Le développement de la polyvalence des équipes de production : Permet de gagner en flexibilité pour pouvoir faire face aux absences inopinées de personnel
- Le travail global sur les flux : Peut permettre de fiabiliser les approvisionnements et de limiter ainsi les risques d'arrêt pour rupture
2) Axe "performance"
Nous avons vu que le taux de performance est principalement impacté par la cadence des équipements.
Ce n'est pas a priori l'axe de travail principal lorsque l'on veut augmenter l'efficacité des équipements, car la perte de cadence, quand elle n'est pas désirée, traduit en général un vieillissement des installations.
Mais si cet élément apparaît comme stratégique afin de pouvoir répondre à la demande des clients, ce travail passera par un projet technique de remise à niveau de tout ou partie de l'équipement.
Quant aux micro-arrêts, ils sont par nature difficiles à quantifier.
Une première étape pour commencer à les éradiquer consiste à recueillir des données sur place afin de les catégoriser et de les prioriser.
3) Axe "qualité"
Le taux de qualité d'un équipement ou d'une ligne de production est directement impacté par les pièces non-conformes qui sont produites.
La démarche permettant d'améliorer le taux de qualité d'un équipement s'appelle "Jidoka" ou "autonomation".
Ce mot, contraction de "autonomy" et "automation" en anglais, traduit l'idée d'intégrer la détection des anomalies dans le processus même de production, de manière automatique.
Il s'agit d'arrêter le travail dès qu'un défaut survient afin d'éviter de produire des séries de pièces défectueuses.
Pour compléter le Jidoka, qui n'est pas toujours simple à déployer, l'application des principes du "Juste-A-Temps" contribuera elle aussi à limiter la quantité de pièces défectueuses en réduisant les quantités de stocks intermédiaires qui pourraient accumuler des quantités importantes de défauts en attente de détection.
Mais prenons à présent un peu de recul et replaçons le TRS dans le contexte du Lean Manufacturing.
TRS et Lean Manufacturing
Dans l'univers du Lean Manufacturing, le TRS joue un rôle crucial dans l'amélioration de la performance industrielle.
Intégré dans la planification et l'ordonnancement de la production, il permet aux entreprises d'améliorer l'efficacité globale de leurs opérations en maximisant l'utilisation des équipements et en réduisant les pertes de temps liées aux périodes de faible performance des machines.
Pour avoir une vision holistique de l'ensemble du processus de production et identifier les domaines d'amélioration, il est également essentiel d'utiliser des outils comme la VSM (Cartographie de la Chaîne de Valeur) qui permet de visualiser et d'analyser les flux de valeur à travers toute l'entreprise.
1) S'attaquer aux pertes
Certaines des actions d'amélioration décrites dans la section précédente attaquent directement des pertes.
C'est par exemple le cas de la TPM, du SMED ou encore du Jidoka.
Pour prioriser et valider la pertinence de ces actions, le TRS constitue ainsi un outil d'analyse tout à fait adapté.
Le seul point de vigilance reste la qualité des données collectées afin de mesurer le TRS.
Au-delà de la valeur absolue du TRS, c'est le suivi régulier de son évolution qui permettra d'identifier certaines dérives.
2) Garder le client comme boussole
Mais malgré son intérêt avéré, le TRS est cependant un indicateur qui est souvent mal utilisé dans l'industrie.
En effet, dans le but de "produire plus", certains sites de production cherchent à augmenter leur TRS à tout prix. Ceci n'est pourtant pas une fin en soi.
Pour le Lean, si l'on cherche effectivement à supprimer les pertes ou gaspillages, la finalité reste de s'adapter à la demande du client.
Plutôt que de "produire plus", il s'agit de "produire mieux", c'est-à-dire au bon moment, dans la bonne quantité, et avec le bon niveau de qualité selon les exigences du client.
Selon les principes du Juste-A-Temps et selon le temps de Takt déterminé par la demande du client, il peut même être nécessaire de réduire volontairement la cadence, et donc le TRS, pour s'adapter à cette demande client.
Conclusion
Le TRS constitue un outil précieux et incontournable dans une démarche de Lean Manufacturing.
Si sa valeur absolue n'est pas pertinente en soi, ce sont surtout le suivi de sa variation et l'analyse de sa décomposition qui vont permettre de s'attaquer aux pertes et de progresser.
Pour donner toute sa valeur, cet outil doit s'inscrire dans une optique plus globale de mise en place du Juste-A-Temps.